Fallos en estructuras de madera. El eslabón débil.
Tabla de contenidos
Numerosos ejemplos de edificios con un papel relevante de la madera van permeando el mercado y en el mundo técnico. Esto a priori es bueno, pero a mayor cantidad de buenos ejemplos, mayor riesgo de fallos.
Los derrumbes de estructuras de madera son negativos para su competitividad en el mercado de la construcción. Cabe una postura fácil ante tales situaciones: «ya lo decía yo, que la madera no era resistente», pero para seguir con la visión positiva, mejor preguntarnos qué se puede hacer para reducir el riesgo de fallos, aprovechar los errores para aprender y evitarlos en futuras obras. Por eso es necesario comprender las causas de estos fallos. En este artículo pretendemos, a partir de varios ejemplos, dar algo de luz en este sentido.
1 Fallo, vulnerabilidad, redundancia y robustez
El fallo de una estructura es la pérdida de su resistencia, rompiéndose o dejando de servir para lo que fue concebida. Viene motivado por hechos que, directa o indirectamente, implican un riesgo para los usuarios, como el colapso general o una rotura local, quedando fuera de esta definición de fallo la pérdida de servicio como los movimientos (deformaciones, vibraciones). Se puede definir la vulnerabilidad como la posibilidad de fallo.
Para paliar el riesgo de fallo, es evidente que hay que focalizar los esfuerzos en hacer buenos diseños y ejecuciones precisas, pero existen además herramientas que ayudan a controlar, hasta cierto punto, el riesgo, como la redundancia [1], o reserva de componentes o de sistemas estructurales sustitutivos, entendida como el establecimiento de mecanismos resistentes alternativos que actúan en caso que el mecanismo principal deje de funcionar. O la robustez, que es la capacidad para resistir un evento extremo sin que el fracaso en la funcionalidad sea completo [2]. Así, una estructura es robusta cuando el fallo de un determinado componente no genera unas consecuencias desproporcionadas.
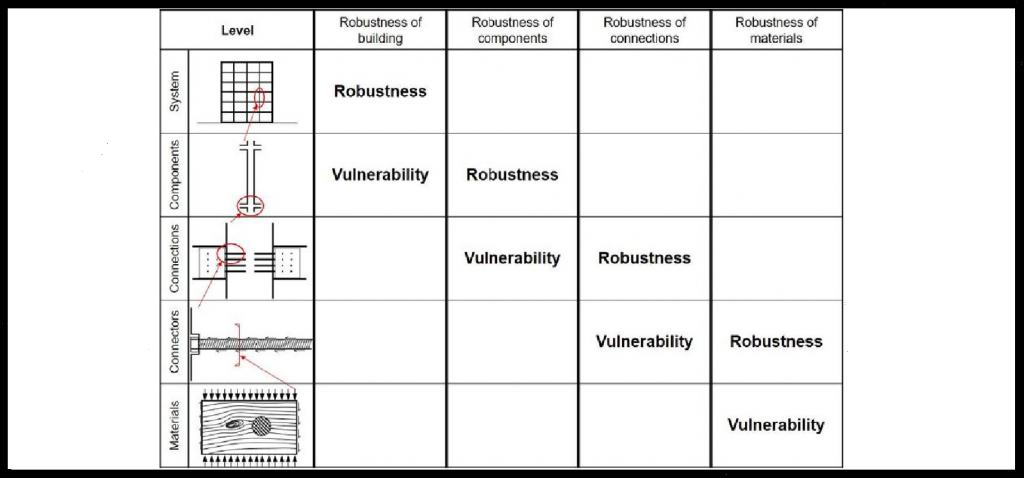
El verdadero reto de la ingeniería de estructuras es la buena gestión del eslabón débil, para evitar que devenga catastrófico.
En los ejemplos que veremos más adelante, queda patente que la vulnerabilidad tiende a concentrarse en las uniones, lo cual es una buena noticia en la medida en que un problema, una vez identificado (y en este caso, además, muy focalizado), es más sencillo controlarlo.
2 Clasificación de fallos
En general, como ocurre habitualmente en patología, el fallo no se puede achacar a un único factor, sino una yuxtaposición de errores y contingencias concomitantes.
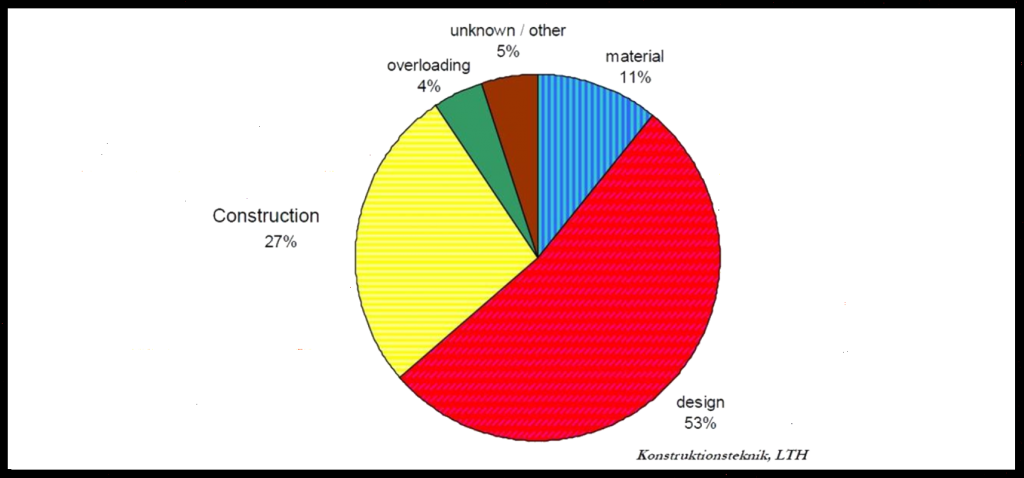
En los estudios consultados, se concluye que la mayor parte de los fallos se podrían haber evitado si los conocimientos disponibles se hubieran utilizado de forma correcta. Dado que alrededor de la mitad de los fallos son causadas por errores de diseño. Una cuarta parte de las fallas se debió a errores cometidos en fase de construcción.
Los diferentes tipos de errores que provocaron fallos en los casos estudiados se clasifican en las siguientes categorías:
- Errores de diseño (53%)
- Diseño deficiente respecto el sistema estructural
- Diseño deficiente respecto la estabilidad lateral de la estructura
- Diseño deficiente respecto las cargas/sobrecargas en el análisis de la estructura
- Diseño deficiente respecto a las acciones medioambientales (por ejemplo, grietas de secado, efectos de contracción y daños de durabilidad)
- Errores de fabricación y obra (27%)
- Principios de fabricación erróneos
- Alteraciones en obra
- Errores de montaje en obra
- Deficiencias del material (11%)
- Capacidad del material
- Desempeño de durabilidad deficiente
- Comportamiento inadecuado de las juntas
- Efectos de la exposición a la humedad (tensiones impuestas, contracción de la madera)
Casi todos los fallos se deben a errores humanos de bulto, los cuales no se evitan incrementando los coeficientes de seguridad, sino mejorando la gestión de los procesos de construcción, control en fase de diseño, así como la formación.
3 Ejemplos
Siemens Arena in Ballerup, Dinamarca (2003), atención a las uniones
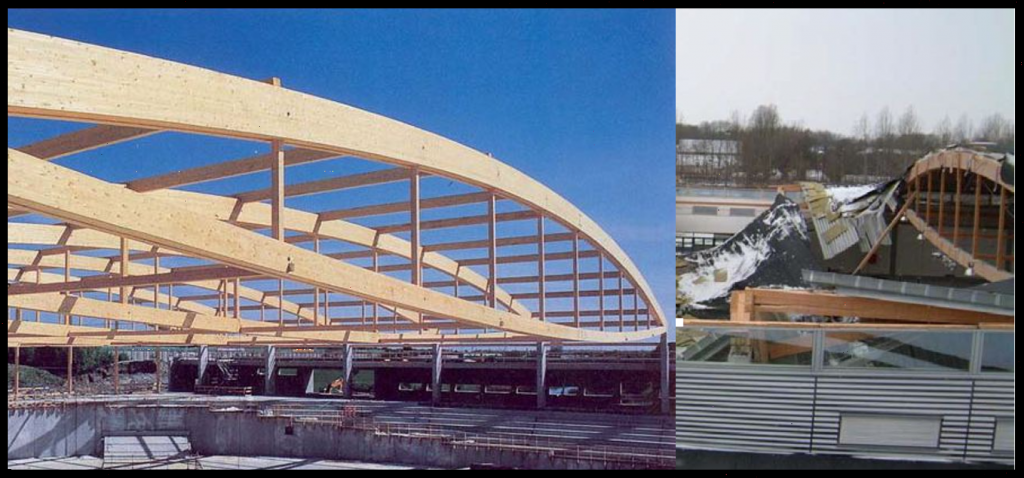
Se trata de una pista deportiva en Ballerup, Dinamarca, inaugurada en 2002, formada por una nave rectangular con 12 cerchas de madera laminada en forma de pez de 72 m de luz y un sistema secundario isostático que evita la redistribución transversal de la carga.
Las cerchas constan de cordones superior e inferior de madera laminada dobles separadas por elementos encolados. La conexión entre cordones cuenta únicamente con montantes verticales, además que quedar unidos en sus extremos en conexiones con placas de acero embebidas y pasadores.
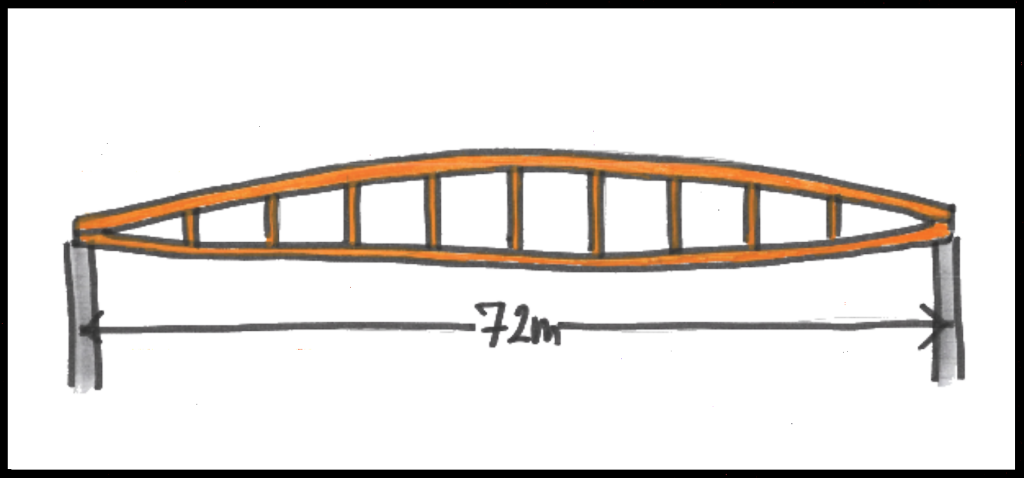
Una noche de enero de 2003, sucedió el colapso parcial de dos cerchas principales de cubierta. No hubo víctimas ni heridos.
A partir del fallo en apoyo por desgarre (splitting) a tracción en par inferior, debido a un error de cálculo humano, se derrumbó parcialmente de repente y sin grietas previas. El colapso comenzó en la conexión entre los cordones superior e inferior de una celosía, lo que provocó pérdida de toda la tensión en el cordón inferior y un colapso inmediato de esa celosía en particular.
El daño se extendió a la celosía adyacente de un lateral, pero se detuvo allí. El sistema secundario isostático y la falta de redundancia, que suele ser una mala práctica para fines de robustez, en este caso evitó que el daño avanzase a otras cerchas, salvando la estructura restante del derrumbe.
En el momento del colapso la estructura solo soportaba su propio peso; el único desencadenante (que no la causa) posible podría haber sido la gran diferencia de temperatura de esa mañana entre el interior de la sala y el ambiente exterior muy frío.
La razón principal del colapso fueron errores graves de diseño en los cálculos de capacidad de las cerchas, así como asumir una resistencia de la madera un 50% mayor que lo que finalmente se usó. A pesar de las necesarias comprobaciones internas, los cálculos nunca fueron revisados por terceros. En total, la capacidad de la cercha rondaba el 25% de lo que debería haber sido por diseño. Dada la pérdida gradual de resistencia de la madera con el tiempo, no es sorprendente que el fallo se produjera de repente después de unos meses, sin ninguna carga adicional. Fue pura suerte que nadie resultase herido.
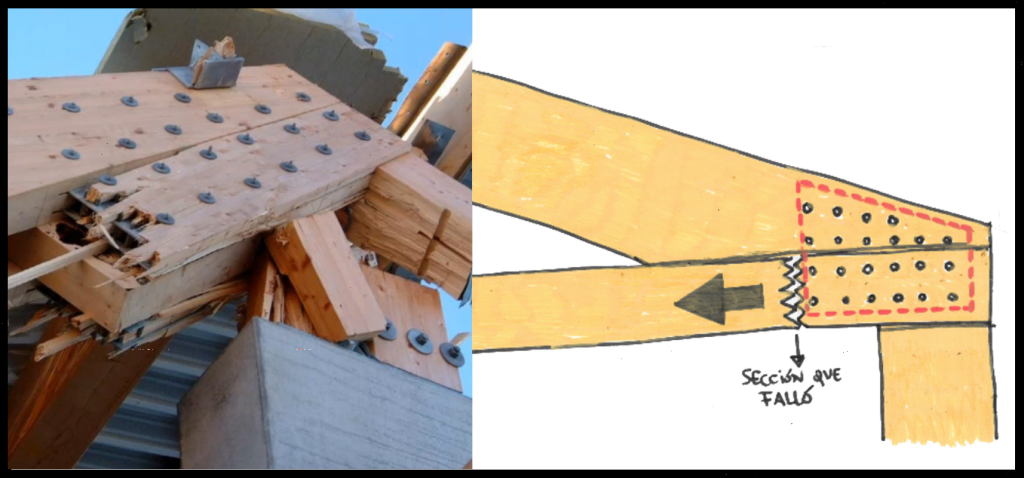
Se identificaron los siguientes errores en el diseño y verificación de la resistencia de la unión:
- En los cálculos se utilizó la sección transversal nominal, sin reducirse por los agujeros de tornillos y las ranuras de las chapas de acero. Sin embargo, en la unión del cordón, las secciones transversales se reducen para permitir la conexión de las vigas superior e inferior. De este modo, el área de la sección transversal se sobreestimó en un 25-30% (ver imagen 8).
- Debido al corte inclinado de los extremos de ambos cordones para su unión, la fuerza normal (centrada en el centro del arco) tenía una excentricidad de unos 50 mm, resultando en un momento de excentricidad, que no se tuvo en cuenta en los cálculos de diseño. El número de clavijas y placas de acero en ranuras da lugar a una unión rígida, resultando en un momento adicional, que no fue considerado en el diseño.
- El diseño de la unión de pasadores fue incorrecto, utilizando una distribución uniforme de la carga en todos los pasadores. Esto da lugar a una sobreestimación de la capacidad de los pasadores entre un 50 y un 100 %.
- El corte inclinado resulta en un ángulo entre la dirección de la fibra y el borde de la viga, reduciendo la tensión y la capacidad del momento de flexión.
- Todos estos factores mencionados anteriormente implican que la capacidad de la primera hilera de clavijas en la viga inferior es solo del 25% al 30% de la capacidad requerida.
- Al mismo tiempo, el efecto de carga fue aproximadamente un 30 a 40% mayor que la resistencia característica (con reducciones debidas a la duración del efecto de carga). El fallo de resistencia en la viga inferior en la posición de la primera hilera de clavijas inició el colapso.
A partir de este accidente se hizo obligatoria en Dinamarca la verificación por parte de terceros, así como medidas de diseño de robustez para estructuras de madera de gran envergadura.
Sala de exposiciones Jyväskylä, Finlandia (2003): error de cálculo y de construcción
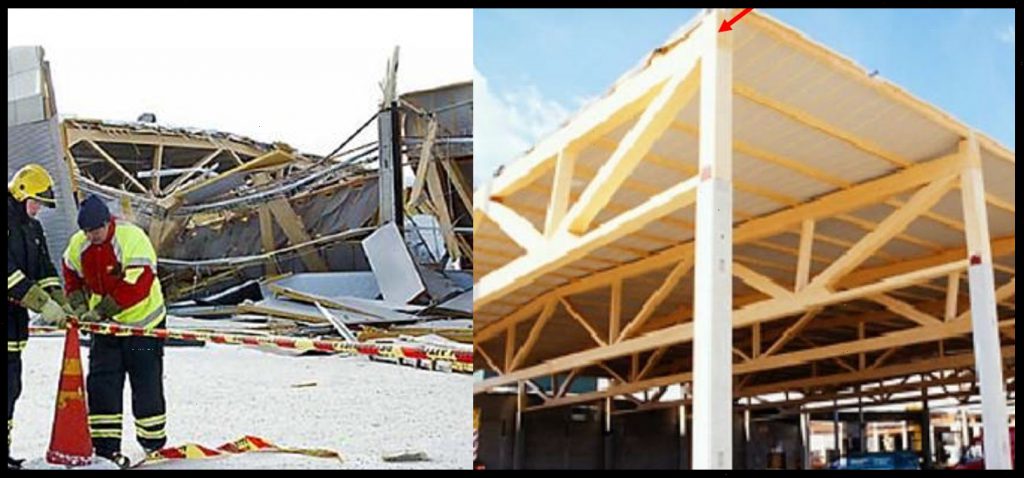
El pabellón de exposiciones Jyväskylä estaba formado por un techo a dos aguas con ligera pendiente. Los soportes del techo en la parte más ancha de la sala eran dobles cerchas de 55 metros de luz de madera laminada de abeto paralelas, unidas con tornillos, dispuestas cada nueve metros, y descansando sobre pilares de hormigón armado, con pernos verticales de conexión.
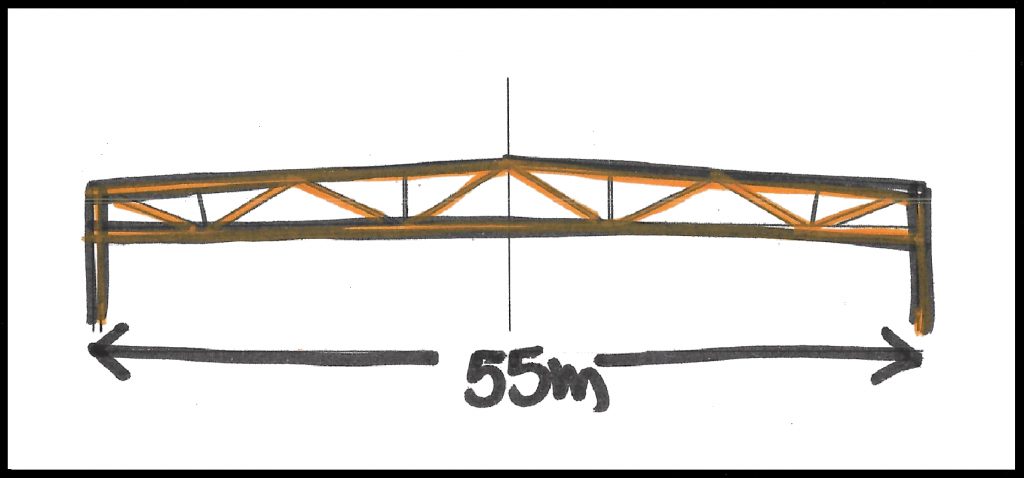
Las cerchas habían sido ensambladas en la fábrica y los componentes de madera debían ser unidos con hasta 48 tacos de acero, según fuera el tamaño de la junta. Los tacos de acero habían sido perforados perpendicularmente a través de dos placas de acero embebidas en la madera.
Las uniones de las cerchas eran con placas y clavijas, con una o dos ranuras aserradas en la madera para colocación de placas de acero de 8 mm de espesor. Tanto la madera como el acero estaban perforados para insertar las clavijas, con los 30 mm extremos sin acero por protección contra incendios del acero de las clavijas.
La mañana de un sábado de 2003, alrededor de dos semanas después de entrar en funcionamiento el edificio, se produjo un accidente con el derrumbe de aproximadamente 2500 m² del techo. El día anterior había terminado una feria educativa y durante la mañana del derrumbe 12 personas trabajaban en el desmantelado de stands. Súbitamente, se escuchó un fuerte golpe en el pasillo, tras el cual alguno de los presentes descubrió que uno de los cordones inferiores de madera laminada de uno de los pares de cerchas se había roto cerca de su apoyo. Entendiendo la inminente posibliidad de colapso, avisaron a los demás para que salieran. Aproximadamente dos minutos después, el par de vigas cayó, junto a los tres pares de cerchas más cercanos y los elementos de cubierta que descansaba sobre ellos. Las 12 personas lograron salir sin que nadie resultase herido.
Ya al comienzo de la investigación del accidente, quedó claro que, según los testigos presenciales, solo había 7 pasadores en una de las uniones de la celosía que primero cedió, mientras que de acuerdo con los planos deberían ser 33. El fallo tuvo sus inicios en este punto debido a la falta de control de calidad en fábrica.
El uso de vigas de madera laminada requiere supervisiones en fábrica, controles de calidad y autorización de la empresa fabricante por organismo acreditado, condición que cumple la empresa que fabricó las celosías de la sala de exposiciones Jyväskylä. Pero no se requiere una supervisión similar en la fabricación de celosías. Los nudos fueron ensamblados en fábrica, excepto los nudos medios de las cerchas, en los que sus conexiones centrales se realizaron en obra porque se entregaron en dos partes para facilitar el transporte.
La calidad de las uniones no era regular: variaba la profundidad de perforación de los orificios para pasadores, la posición de estos era inexacta, su profundidad variaba en aproximadamente ±1,5 cm respecto lo previsto, hubo errores de alineación de las placas, los agujeros para los pasadores estaban bastante flojos (se podían mover con la mano), el ancho de las ranuras para las placas era en muchos puntos muchos milímetros más anchos que el grosor de la placa y la longitud de las clavijas también difería en más de 10 mm.
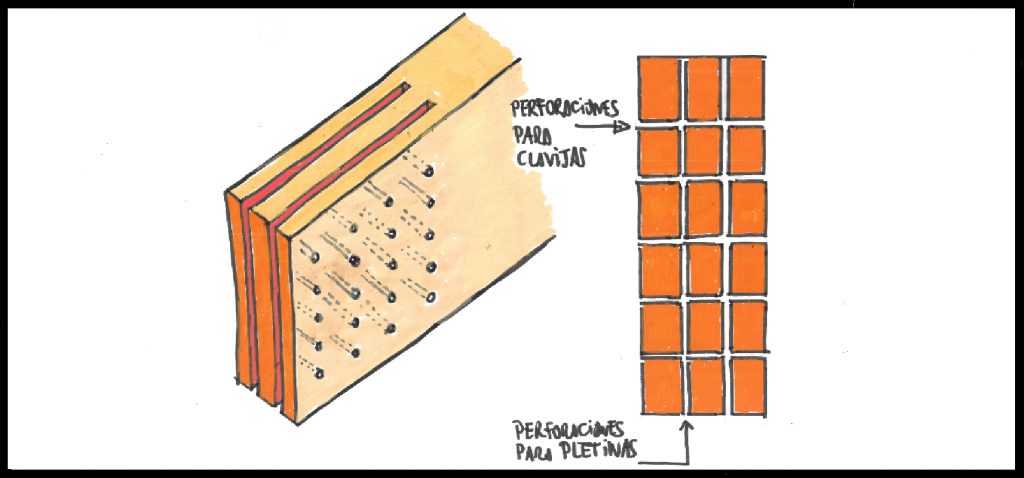
Las condiciones meteorológicas (temperatura, lluvia, viento y nieve), no presentaban rangos especialmente destacables en el momento del accidente. El espesor de nieve en la cubierta correspondía a unos 50 kg/m2, cuando una estructura de techo válida debería soportar más de cuatro veces dicha carga. La carga utilizada en el diseño sin carga de viento está por encima el peso propio mencionado de 1,0 kN/m2 y la carga de nieve calculada es de 2 kN/m2, es decir, un total de 3 kN/m2, valores que comparados con la carga en la situación del accidente, arroja que la carga era aproximadamente el 50% de la carga de diseño.
Incluso si se hubieran fabricado correctamente, la capacidad de las juntas de clavija no habría sido suficiente porque el diseño no había tenido en cuenta la fractura por desprendimiento de los pasadores de la unión (de nuevo el splitting). Así, el techo habría colapsado sobre unos 2 kN/m2 con carga de nieve, que estadísticamente ocurre una vez cada 50 años.
Quienes participaron en el proyecto de construcción estaban calificados y tenían experiencia. Sin embargo, la fragmentación del proyecto en tareas independientes aumentó la posibilidad de errores. Así, una conclusión importante es que las fases de trabajo que afectan a la seguridad no deben quedarse solo en una organización o en una pequeña parte de una organización.
Dos razones son esenciales para entender este colapso, la ausencia de cualquiera de las cuales lo habría evitado:
- La mala calidad de las uniones de pasadores y especialmente la ausencia de 26 clavijas de uno de los 32 pares de celosía de la articulación esencial
- La ausencia de un análisis de fractura por rotura en bloque por desgarro de las directrices de diseño europeas para estructuras de madera y, por tanto, debido al diseño de las juntas de clavija de las cerchas de cubierta en cuestión.
Bad Reichenhall, Alemania (2006): el pegamento que dejó de pegar
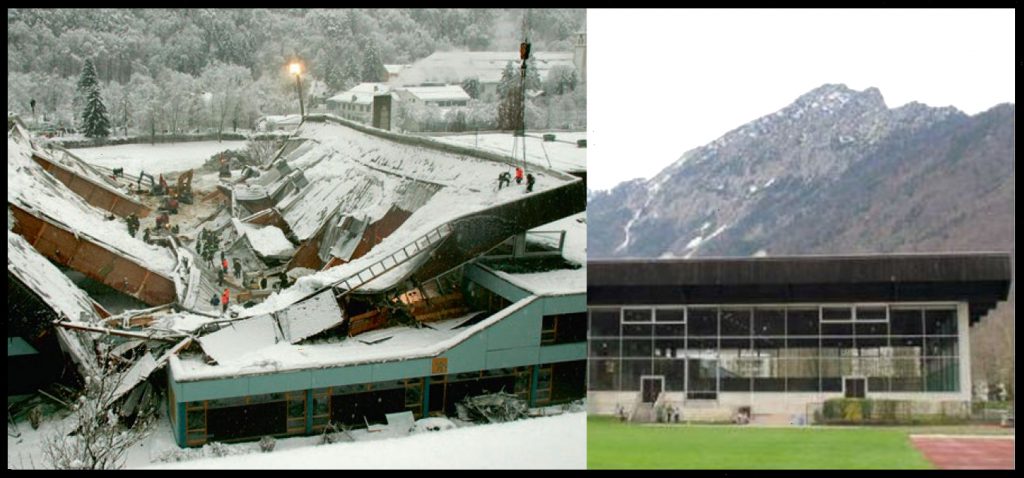
Se trata de un pabellón polideportivo construido en 1972, con una cubierta de gran envergadura con vigas cajón de madera de 48 m de largo y 2,87 m de altura y un sistema de vigas secundario. Su construcción fue única, al no recurrir a la típica construcción con madera laminada, y optar por el uso de vigas cajón con alas superiores e inferiores laminadas, conectadas con tableros de alma encolados.
Se alcanzaron los 48 metros con tres tramos de 16 m de largo conectados con finger-joints. Las vigas principales estaban conectadas con un sistema secundario rígido de correas, actuando las veces de arriostramiento lateral, que posibilitaban la transferencia de carga entre las vigas principales, sin tener en cuenta la robustez estructural. Es decir, la estructura se comportó como una cadena en la cual el colapso del primer pórtico arrastró al resto de elementos.
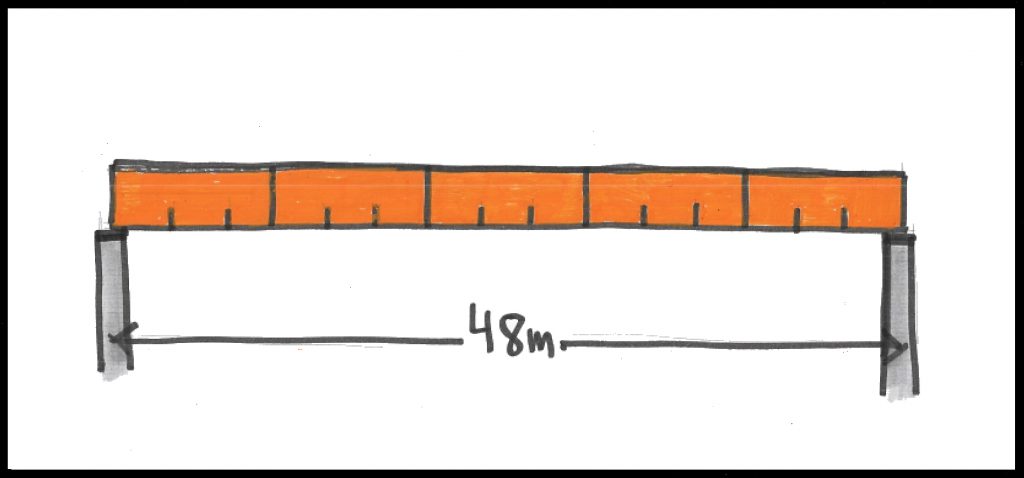
La sala cumplió su propósito durante 34 años, pero con insuficientes trabajos de mantenimiento, persistiendo problemas como las goteras, los cuales en los días previos al derrumbe, ya generaron preocupaciones sobre la seguridad estructural, lo que llevó a la cancelación de las sesiones de entrenamiento a raíz de las tormentas de nieve. En un día particularmente nevado, el techo se derrumbó mientras el pabellón estaba abierta al público, con una carga de nieve, aunque elevada, por debajo del valor característico, causando 15 fallecidos, entre ellos 8 niños, y hasta 30 heridos, convirtiéndose en uno de los mayores derrumbes en Alemania después de la Segunda Guerra Mundial.
Múltiples razones llevaron a este colapso catastrófico. El fallo empezó con la viga cajón principal por degradación de colas no resistentes a la humedad en un entorno exigente y mantenimiento insuficiente, lo que llevó a la reducción de la capacidad de las uniones, seguido del colapso de toda la cubierta debido a la conexión rígida entre las cerchas, el cual facilitó que el avance del colapso a toda la estructura.
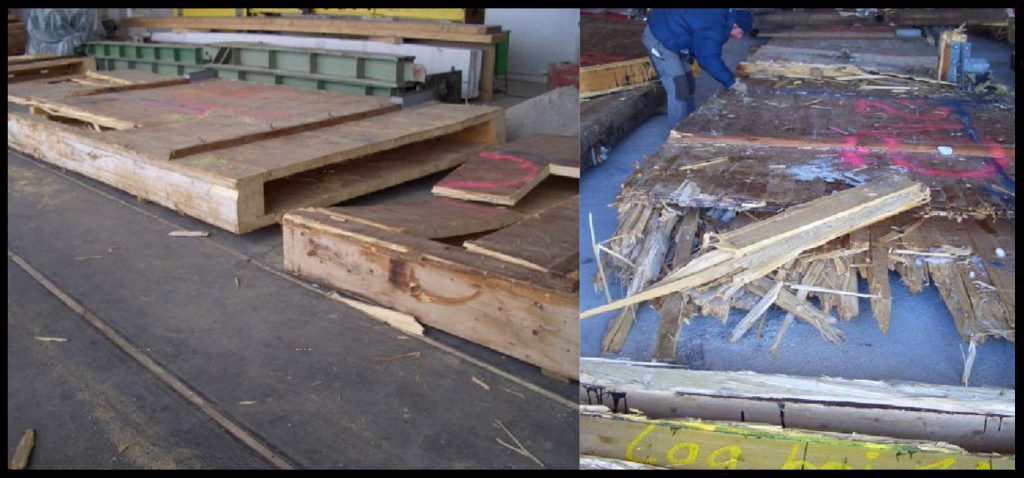
Ciertos errores en el cálculo estructural de las vigas cajón principales agravaron esta situación crítica: no verificación de la resistencia a la tracción en el centro de gravedad de las vigas y no tener en cuenta la reducción de capacidad debida a las uniones entre tramos con finger-joints. Todo lo cual llevó a un factor de seguridad de alrededor de 1,5, por debajo del 2,0 requerido. Si el diseño hubiera sido revisado por otro técnico (según el “principio de los cuatro ojos” que es obligatorio en Alemania, para tales estructuras especiales pero no se hizo en este caso), el inicio del daño podría haberse retrasado o incluso evitado.
Por otro lado, hay que tener presente la elevada exigencia de las condiciones ambientales en los pabellones de hielo, particularmente si no cuentan con sistemas de climatización. La alta humedad relativa y la condensación en la parte inferior de las cerchas condujeron a una degradación significativa de la cola en juntas, lo que a su vez condujo al inicio del colapso con carga de nieve no especialmente elevada.
Otra razón importante del colapso fue el uso de adhesivo de urea-formaldehído, no adecuada para ambientes húmedos, en las uniones de los finger-joints y la unión entre las alas de la viga cajón y las placas de almas. En el momento de la construcción no se contemplaban estas limitaciones en la normativa. Por otro lado, inspecciones y mantenimiento mucho más rigurosos habrían posibilitado la detección de estas degradaciones mucho antes de que pudieran volverse peligrosas.
La razón principal de la desproporcionalidad de las consecuencias fue la conexión rígida entre las vigas principales: una vez que una de ellas comenzó a colapsar, la carga se redistribuyó a las vigas adyacentes, lo que provocó un colapso progresivo tipo cremallera de toda la cubierta. La robustez estructural no se analizó con suficiente rigor en el diseño, a pesar de que este hiperestatismo debería proporcionar caminos de carga alternativos que, en principio, mejoran la robustez.
Por último, pero no menos importante, la aprobación técnica para el diseño de las vigas cajón solo existía para cantos de hasta 1,20 m, mucho menor que las vigas de 2,87 m de canto en este caso. Esta ampliación del concepto de diseño sin verificaciones de casos específicos puede haber contribuido al colapso.
Las principales lecciones aprendidas de esta tragedia son:
- Realizar un correcto plan de mantenimiento
- Proteger las estructuras de exposiciones sistemáticas (por ejemplo, con compartimentación);
- No usar cola de urea-formaldehído en condiciones de humedad variable
- Revisar el diseño (el “principio de cuatro ojos”) e inspeccionar y mantener durante toda la vida útil de la estructura.
En el siguiente vídeo se relata el suceso: https://www.youtube.com/watch?v=z8MKilbJal0
Puente Perkolo, Noruega (2016): cargas infravaloradas en la junta
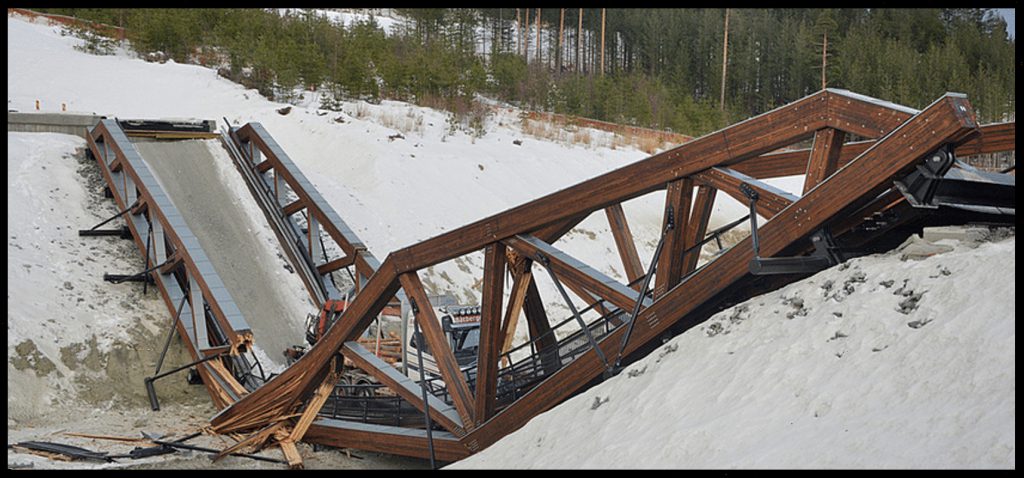
Este puente de carretera estaba ubicado en Sjoa en Gudbrandsdalen, Noruega, y se abrió al tráfico en octubre 2015. Constaba de dos cerchas de madera laminada de 47,5 metros de luz, que soportaban, por medio de una serie de vigas transversales de acero, una plataforma de madera laminada. Fue diseñado de acuerdo con los Eurocódigos.
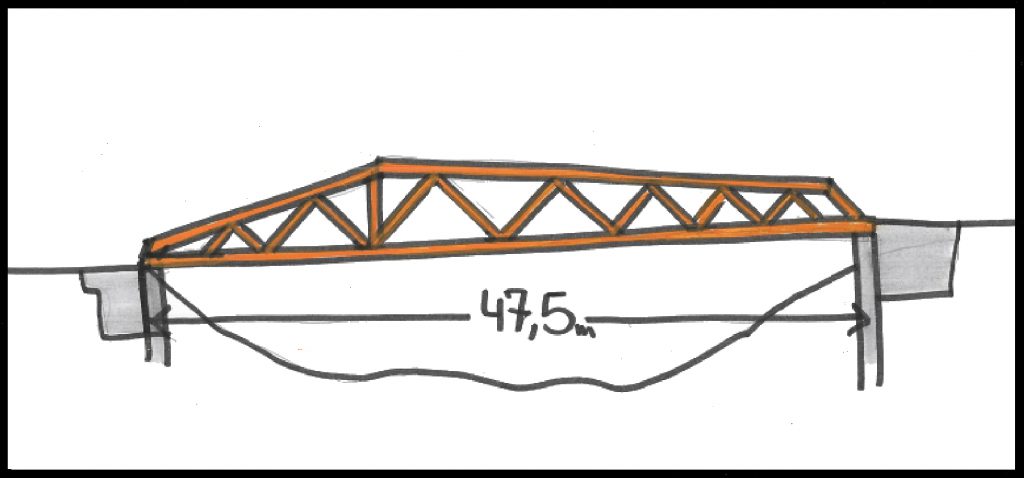
El cordón inferior estaba formado por tramos unidos mediante 4 placas de acero ranuradas (de 12 mm de espesor) y 24 tacos de acero en 6 filas a lo largo de la dirección de la fibra, de Ø12 mm. Se cree que las placas se asientan en ranuras de 14 mm de ancho.
El puente Perkolo se derrumbó el 17 de febrero de 2016, mientras un camión maderero con un peso estimado de 300 kN cruzaba el puente. Se determinó que la carga en el puente en el momento de la falla fue aproximadamente un tercio de la carga para la que se había diseñado el puente.
Las investigaciones realizadas tras el derrumbe determinaron que la causa principal fue un error severo relacionado con el diseño de una junta a tope entre tramos del cordón inferior. Al diseñar un nodo de una celosía, la diferencia en la fuerza axial entre la izquierda y la derecha del nodo generalmente determina el número de conectores que se adoptarán en el cordón de la celosía. Esto es cierto, sin embargo, solo si el cordón es continuo. En el caso de que se interrumpa la continuidad, es decir, por la presencia de una junta de montaje, como fue el caso de la junta fallida del puente Perkolo, el número de conectores debe derivarse sobre la base de la fuerza máxima de ambos valores. El error fatal aquí fue que la junta de montaje se diseñó como si el cordón inferior hubiera sido continuo, es decir, para una fuerza axial N=Nb‐Na, en lugar de una fuerza axial correspondiente a la mayor entre Nb y Na.
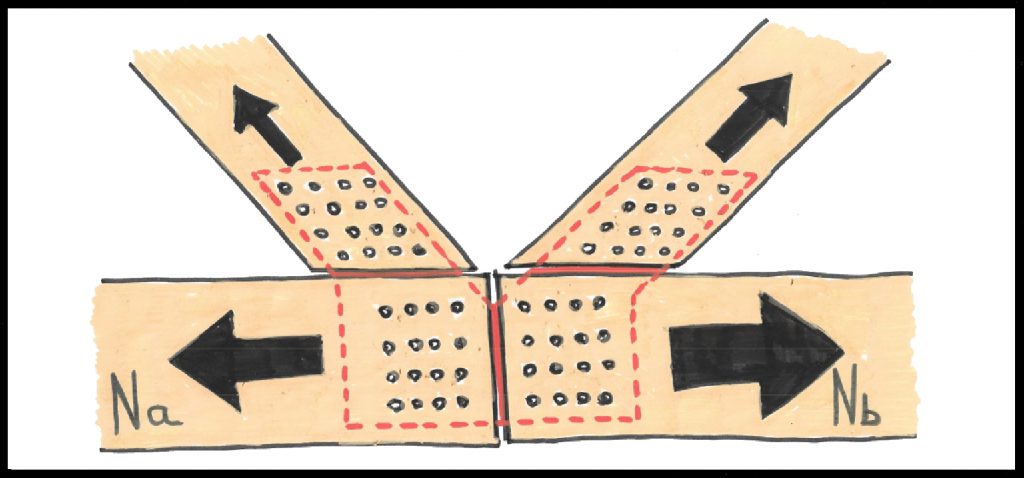
Al calcular la capacidad característica para un pasador aparecen planos con doble cortadura según los modos de fallo según se muestra en la figura 7 (j/l, k y m).

La investigación ha revelado un grave error de diseño. Si comparamos la capacidad de diseño con el efecto de la carga de diseño, 3190 kN, vemos que la capacidad calculada de la unión es solo aproximadamente un 28% del efecto de la carga característica (1275 kN) es la real de la capacidad de la junta.
Dichos errores no deberían ocurrir, pero ocasionalmente incluso los ingenieros expertos pueden ser víctimas por el tipo de «cortocircuito» que ha tenido lugar aquí. Lo que hace que el asunto sea particularmente grave es que el error no fue detectado, sino que se mantuvo hasta que provocó el colapso del puente. El hecho de que el derrumbe se produjera antes de que se abriera al tráfico, y no causó heridos graves, es un escaso consuelo.
Aparte del hecho de que la unión es demasiado pequeña, también es una mala solución colocar la unión entre tramos en el nudo. Para obtener la capacidad suficiente en la junta tal como se dispuso, se debería cuadruplicar el número de clavijas, es decir, hasta 100 clavijas, lo cual implicaría una conexión demasiado larga, resultando más simple y eficiente si esta se dispusiera entre dos nudos.
Así, las uniones entre tramos de elementos laminados con cargas elevadas no deben colocarse en los nudos, especialmente cuando los componentes que se conectarán al componente que se unirá tienen un ancho menor que este. Al colocar la unión en un área donde el componente no se ve afectado por otros elementos, se obtiene una unión simple, clara y eficiente, y cualquier unión también será significativamente más fácil de dimensionar.
Esta revisión también ha revelado varias debilidades:
- Las juntas entre elementos de madera con grandes solicitaciones no deben colocarse en las uniones.
- Se realizaron trabajos de soldadura defectuosos.
- El arriostramiento lateral de las cerchas no es muy efectivo.
- No es posible la inspección visual de las uniones con placas embebidas. Por lo tanto, es recomendable el uso de acero inoxidable, y diseñar conexiones que no se comporten de manera dúctil en la mayor medida posible.
- La Dirección de Caminos de Noruega debe velar para hacer cumplir los requisitos para la documentación presentada de una manera más clara, pero la gestión de la información no lo facilita: 1236 páginas repartidas en tres grandes carpetas, no parece lo más apropiado para el control de un proyecto como este. Desafortunadamente, esto no es inusual.
- En el uso de programas informáticos, los resultados de estos deben evaluarse de manera muy crítica por parte de técnicos especializados.
Puente Tretten, Noruega (agosto 2022), tensiones en la unión
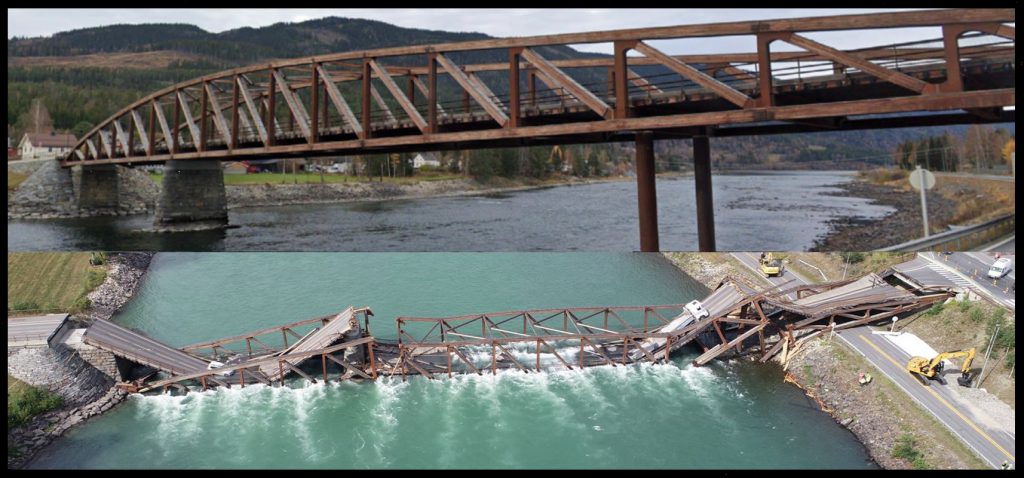
El puente para tráfico rodado cerca de la población de Tretten, inaugurado en 2012, colapsó en agosto de 2022, al paso de un camión cargado de leña, sin causar víctimas más allá de heridas en el conductor del mismo.
Tenía una longitud de 148 metros con un vano principal y dos vanos laterales, con un estribo de hormigón en un extremo, un soporte de piedra en el río, y otro soporte de madera en una de las orillas. El tablero del puente se apoya en el borde inferior de dos vigas en celosía de altura descendente. Las verticales son de tubo de acero, las barras del borde superior y las diagonales son de madera laminada. Por lo tanto, es un puente con predominio de la madera. Los cordones superiores de las cerchas se apoyan únicamente sobre las 5 celosías intermedias del vano principal perpendiculares a su plano con riostras en K. Llama la atención que las diagonales estén todas dispuestas en el mismo sentido, por lo que están sometidas tanto a compresión como a tracción.
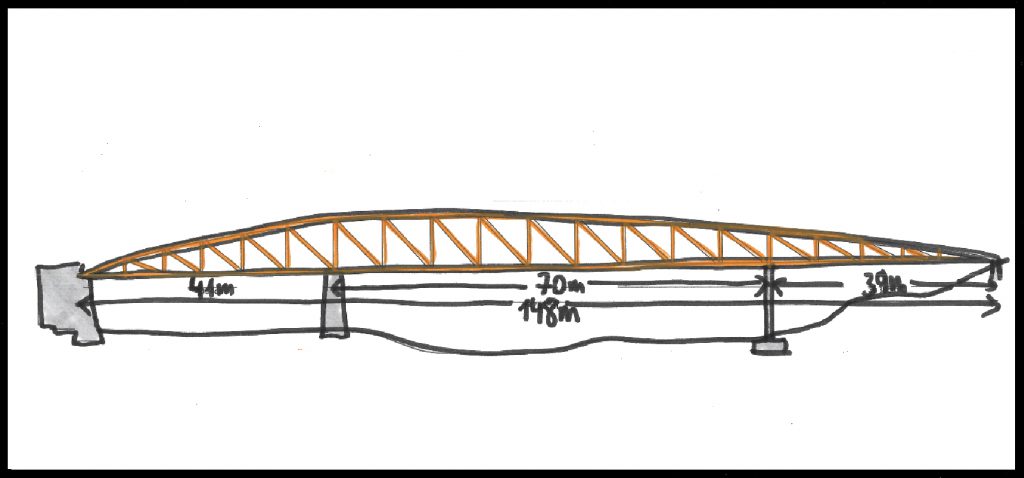
El puente Tretten fue inspeccionado junto con todos los demás puentes de vigas de madera tras el colapso del puente de Perkolo en 2016, también en Noruega.
Antes del derrumbe, los usuarios de la vía reportaron una especie de balanceo cuando estaban en el puente, al mismo tiempo que vehículos más grandes. El puente se sometió a una inspección exhaustiva en 2021 y a una inspección más simple en junio de 2022, sin que se detectaran fallas.
Se apunta como posible causa del colapso la conexión borde superior de una de las diagonales. Las investigaciones técnicas acreditan que la causa inicial de los daños del derrumbe del puente de Tretten fue la rotura de una de las diagonales del vano principal.
La forma de fractura se identifica como una falla por corte de bloque entre la parte de madera y el acero/clavijas en la unión. Esta es una forma momentánea de falla que puede causar la sobrecarga de otros elementos en la armadura con la carga posterior y, como resultado, el colapso del puente. La forma de la fractura está respaldada tanto por exámenes técnicos de las partes de la fractura, material fotográfico y observaciones de testigos, como por análisis y cálculos estructurales realizados.
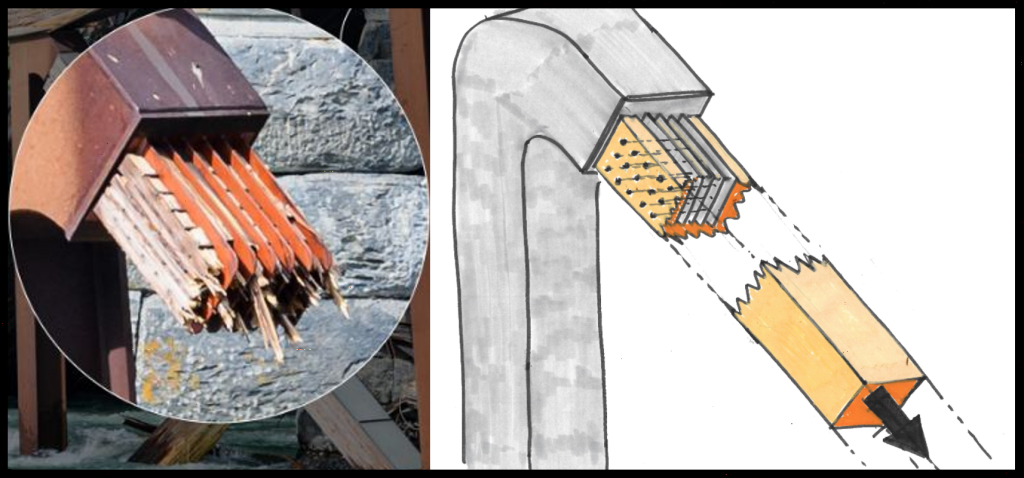
Sugerente análisis del fallo del puente: [14] https://www.youtube.com/watch?v=FSPI0xkTifI
Hasta el momento se ha evaluado que la causa de la forma de fractura es una sobrecarga importante en relación con el impacto de la carga y la capacidad portante del puente, en lo que respecta a la falla por cortante del bloque en las conexiones a dichas diagonales. Comprobado según los métodos de cálculo recomendados en la normativa vigente en la actualidad para el diseño de estructuras de madera, el grado de aprovechamiento en las conexiones en las correspondientes diagonales se situó en torno al 200%. Es decir, la capacidad de estas conexiones era la mitad de lo que deberían haber sido al calcular el estado límite de falla del puente, donde se tomaron en cuenta factores de seguridad tanto para las cargas como para la resistencia de los materiales.
4 Conclusiones
Analizados estos ejemplos, queda destacado que el fallo por desgarre (splitting) longitudinal se repite en 4 de las 5 estructuras analizadas. El eslabón que falló en estos 4 casos es una unión tipo placa y clavijas incorrectamente dimensionada, agravados por cuestiones de diseño, ejecución y mantenimiento.
Se trata de grietas longitudinales causadas por tensiones perpendiculares a la fibra, en la mayoría de casos generadas (y agravadas entre otras causas concomitantes como la podredumbre, ausencia de redundancia, hiperestaticidad, oxidación, fatiga…), por solicitaciones elevadas en las uniones, que llevan a la concentración de tensiones en los conectores/pasadores de acero, las cuales generan las tensiones perpendiculares a la fibra en la madera. Así, hay que priorizar el diseño y comprobación de estos eslabones débiles en las uniones.
Significativamente, estos 4 casos el fallo se produjo de forma inmediata a la entrada en uso de las estructuras, mientras que el caso cuyo causa es distinta (el caso de Bad Reichenhall en Alemnaia, en el que fallaron las colas y por errores de elección, dimensionado y mantenimiento). También este caso, en el que la estructura se mantuvo en uso durante más de 40 años, es el único en el que desgraciadamente hubo víctimas.
Así, se puede concluir que la mayoría de fallos, tanto de los estudios citados, como de los ejemplos expuestos, son en fase de diseño de proyecto, lo cual lleva a poner el foco en estos puntos:
- En primer lugar, poner de manifiesto que los errores humanos son bastante comunes (ya sea por formación inadecuada, carencias profesionales, errores, descuidos, simplificaciones erróneas y asunción de riesgos para ahorrar tiempo y/o dinero).
- Es necesario proporcionar formación específica para la diligencia de técnicos en los problemas especiales en ingeniería de la madera. La formación y la capacitación son las únicas maneras efectivas de minimizar los errores.
- Igualmente, la divulgación de guías, manuales y normativas para el diseño de estructuras de madera, incluyendo soluciones correctas e incorrectas, enfocándose en puntos críticos típicos.
- Hay que disponer de información sobre casos de fallo, para aprender de los errores.
- Aplicación del principio de los 4 ojos: más de un técnico u organización debe revisar los diseños y cálculos más comprometidos.
A los fallos de diseño, les siguen los implicados en fase de ejecución. Para minimizarlos, hay que centrarse en:
- Mejorar el control de calidad para la estabilidad general tanto durante el montaje como en los edificios terminados.
- Para asegurar un estándar de calidad adecuado de las instrucciones europeas de planificación y diseño, se recomienda generar un sistema de montaje, mantenimiento y monitorización correspondiente que permita una respuesta rápida a cualquier error o deficiencia crítica para la seguridad.
A modo de guía, dadas las conclusiones de los ejemplos vistos, y más allá de las recomendaciones expuestas, se destacan una serie de aspectos de diseño que por delicados se deben tratar con especial atención:
- Dar importancia al correcto diseño de uniones y juntas.
- Arriostramientos para evitar problemas de inestabilidad, pandeo lateral, tanto en la estructura terminada como durante la construcción.
- Prestar atención a situaciones con riesgo de fallo perpendicular a la fibra.
- Consideración de los efectos de la humedad y correcto mantenimiento.
- Evitar muchos actores involucrados en el proceso de construcción, quedando poco definida la responsabilidad general del sistema.
- Documentación integrada de la estabilidad y capacidad de carga, de fácil acceso, que permita el control de terceros.
- Es necesario regular la presión de tiempo de realización de proyectos.
5 Fuentes bibliográficas
- [1] https://victoryepes.blogs.upv.es/tag/redundancia/
- [2] Voulpiotis, Konstantinos Robustness of Tall Timber Buildings, Doctoral Thesis, ETH Zurich, 2021.
- [3] Frühwald, E., Fülöp, L., Toratti T., Thelandersson S. «Robustness evaluation of failed timber structures, Meeting of COST Action TU 601 (Robustness of Structures)», Zürich, Switzerland, 4-5 february 2008.
- [4] Jørgen Munch-Andersen, Philipp Dietsch, «Robustness considerations from failures in two large-span timber roof structures», COST Actions, Lubljana, 2009.
- [5] Sven Thelandersson, «Why do structural failures occur?», Lund University,
- [6] Hansson, Eva Frühwald, «Analysis of structural failures in timber structures: typical causes for failure and failure modes», Suecia, 2011.
- [7] Frese, M., Blass, H.J. «Failure analysis on timber structures in Germany, A contribution to COST Action E55, Modelling of the Performance of Timber Structures», Graz Meeting, may 14/15, 2007.
- [8] Johansson C-J., Camilla Lidgren C., Nilsson Ch., Crocetti R., «Takras Vintrarna 2009/2010 och 2010/2011 – Orsaker och förslag till åtgärder (Roof collapses winter 2009/2010 and 2010/2011 – reasons and proposals for actions), Suecia, 2011.
- [9] VVAA. «Kollapsen av Perkolo bru – hva gikk galt?», Bruseksjonen i Vegdirektoratet, Statens vegvesen, Noruega, 10 marzo 2016.
- [10] Ivar Björnsson, Roberto Crocetti, Martin Fröderberg and Anders Klasson, «Is advanced structural modeling always synonymous, with increased accuracy?», Division of Structural Engineering, Lund University, Sweden, 2016.
- [11] Andrea Roncari, Cristiano Loss, «Creos-laminated timber building equipped with ductile muliple shear slotted-in steel plates connectoin proof of concept», sWorld Conference on Timber Engeneering 2021, Santiago de Chile, 2021.
- [12] Wolfgang Seibel, «Politicization of the Non-politicizable: The Collapse of the Ice Skating Rink in Bad
- Reichenhall on 2 January 2006″, Palgrave Macmillan, Konstanz, 2022.
- [13] VVAA. «Information document #2: Preliminary ionverstigation of the collapse at Tretten on 15 August 2022», Norwegian Safety Investigation Authority, Lillestrøm, 2 December 2022.
- [14] https://www.youtube.com/watch?v=FSPI0xkTifI
Oriol Palou
También puede interesarte