PABELLÓN DE MADERA BUGA: MÁS ALLÁ DEL CONTROL NUMÉRICO
Tabla de contenidos
El pasado diciembre tuvimos el placer de asistir a la 25º edición del FORUM HOLZBAU INTERNACIONAL, celebrado en Innsbruck (Austria). En él pudimos conocer las últimas novedades del sector de la construcción en madera de Centroeuropa.
Uno de los proyectos que más nos fascinó fue el «Pabellón de madera BUGA», este ejemplo arquitectónico muestra las posibilidades de una construcción en madera eficiente, económica y expresiva que surge de la artesanía, la innovación digital y la investigación.
BUGA
El pabellón de madera BUGA se localiza en Heilbronn (Alemania), en la isla de verano del Federal Garden Show 2019.
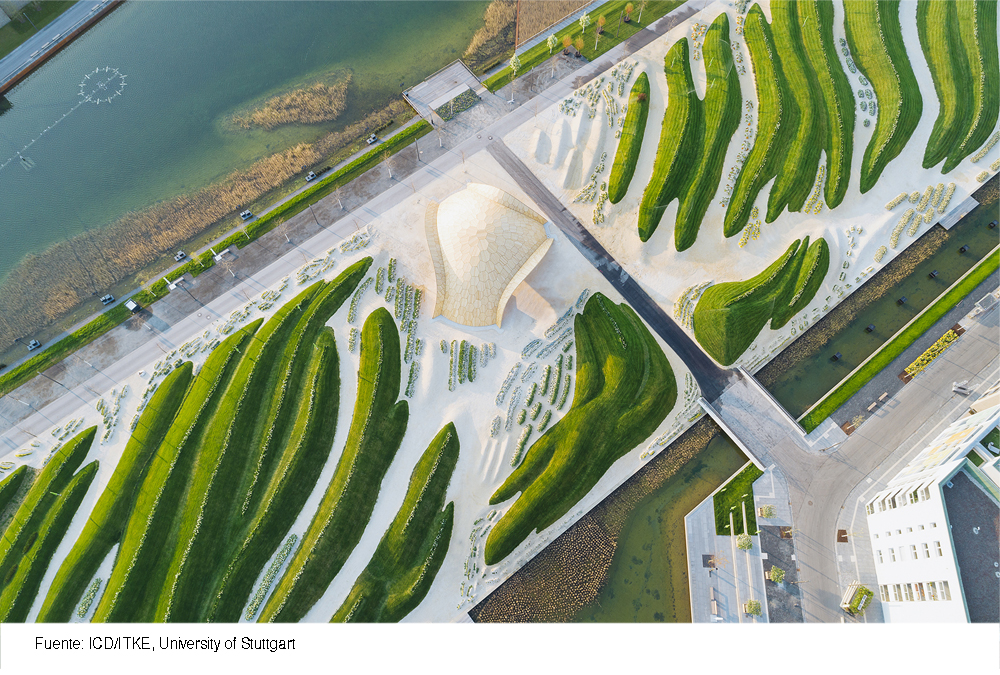
Las aberturas de sus tres arcos direccionan al visitante a su interior, mostrándole un espacio con una excelente acústica y una atmósfera arquitectónica idílica para eventos y quedadas.
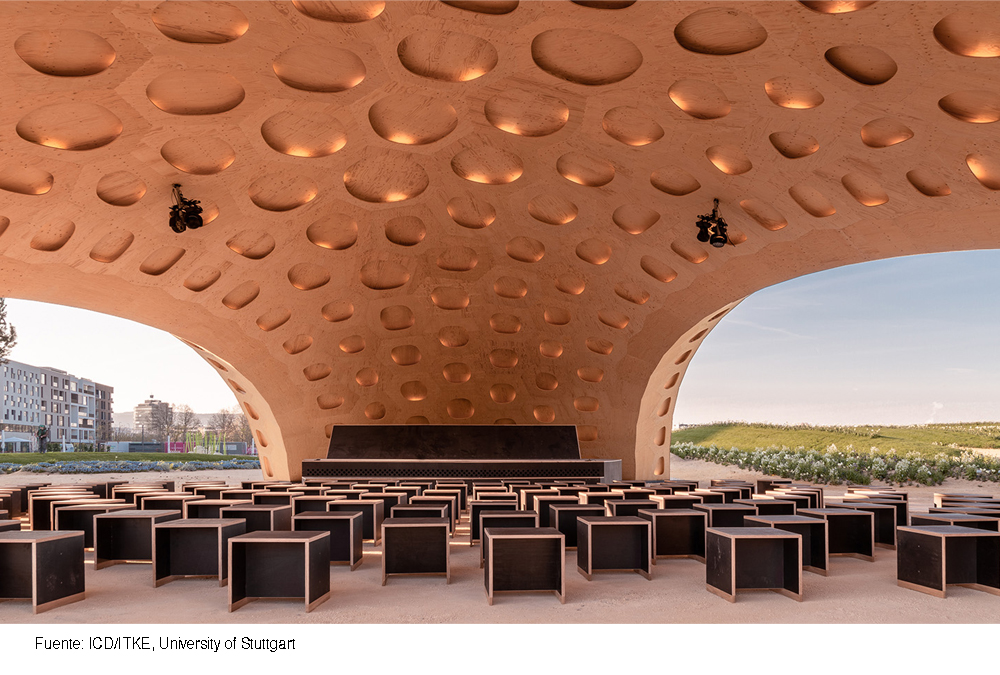
Origen
El diseño del pabellón desarrollado conjuntamente por el Institute for Computational Design and Construction (ICD) y el Institute for Building Structures and Structural Design (ITKE) de la Universidad de Stuttgart se fundamenta en la biometría, en las medidas estandarizadas de los seres vivo o de los procesos biológicos. El objetivo de este concepto es utilizar a nivel multiescalar «menos material» a través de «más forma». El apoyo en este principio biométrico no es casualidad, durante casi una década el ICD y el ITKE han estudiado los principios biológicos del esqueleto de los erizos de mar.
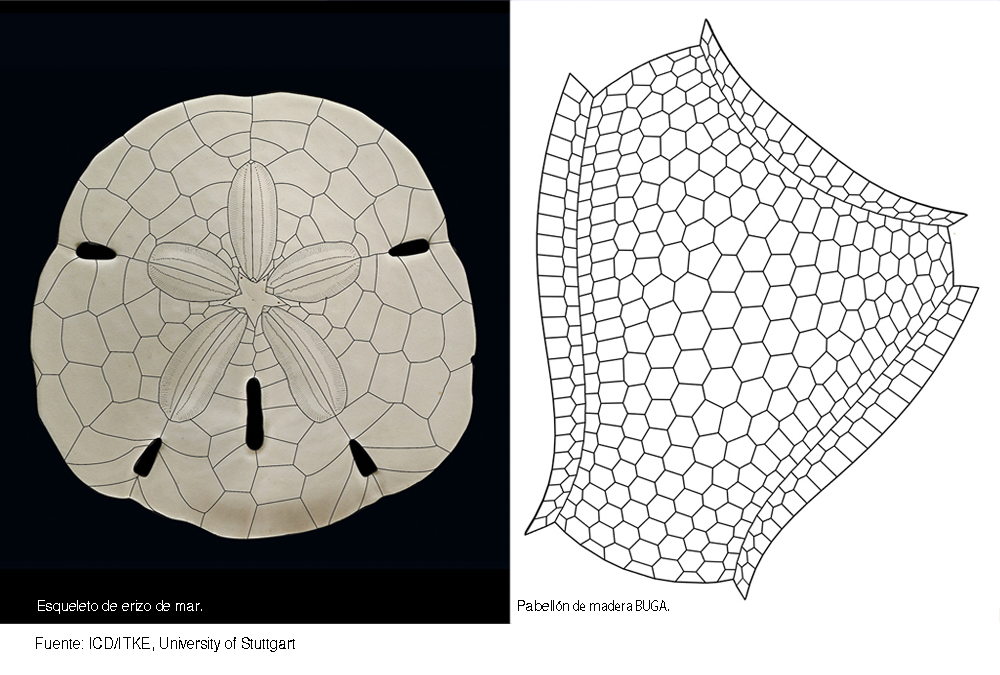
Esta investigación ya se puso en práctica en 2014 en el Pabellón Forestal en Landesgartenschau en Schwäbisch Gmüd.
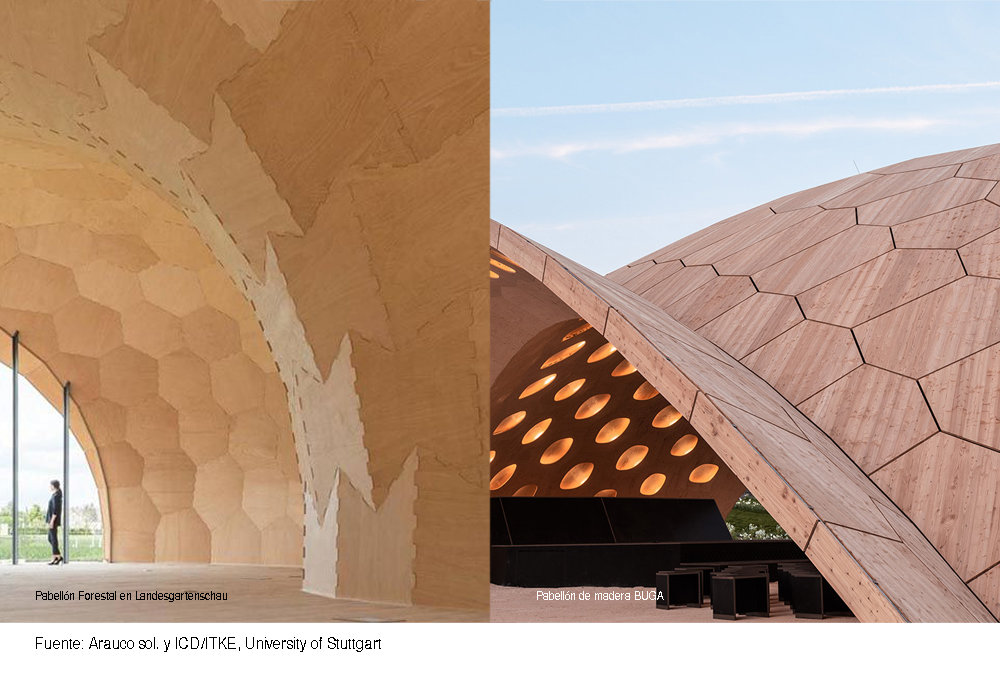
En 2019, con el Pabellón BUGA, se ha conseguido con el mismo diseño arquitectónico que el Pabellón de Landesgartenschau mayor rendimiento estructural de cada una de las piezas que lo constituyen. Con igual cantidad de madera por metro cuadrado se alcanza el triple de luz, y se logra la reutilización integral del proyecto, pudiendo cambiar su ubicación sin perder sus características estructurales.
Diseño.
El pabellón BUGA es un proyecto pionero en el aprovechamiento de las nuevas tecnologías, debido a su enfoque multiescalar consigue tener en cuenta simultáneamente aspectos tanto arquitectónicos como estructurales, lo que le permite desarrollar el proyecto en poco más de un año, con una elevada precisión.
El proyecto está formado por 376 piezas de placa distintas, constituidas por componentes individuales planos, con 17.000 uniones diferentes entre ellas, de acuerdo a los requisitos de contorno geométricos individuales y al diseño global. La forma de cada componente del pabellón está determinada por el diseño, por la producción robótica y por los requerimientos estáticos del proyecto. Las complejas geométricas tridimensionales de los componentes y las geometrías de conexión que varían en toda la carcasa imponen una gran demanda en la planificación y el cálculo estático. Se requieren interfaces informáticas, similares a BIM, y el uso de herramientas de planificación paramétrica para administrar la gran cantidad de información.
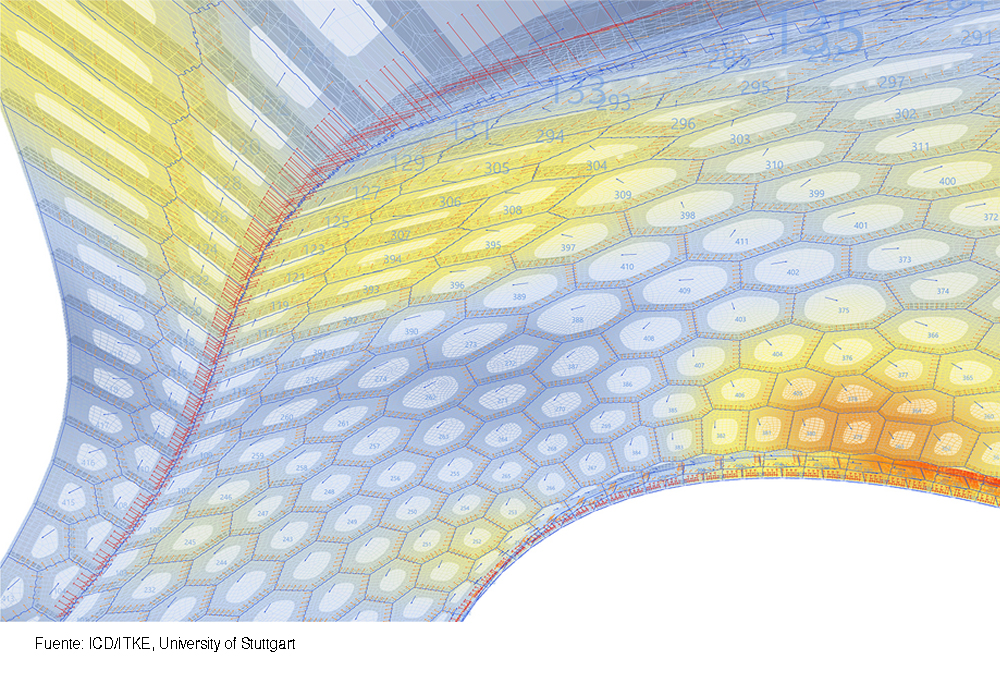
La planificación paramétrica también permite la retroalimentación para la optimización estática de la geometría global de la carcasa, la disposición de los segmentos, las geometrías de apertura, los grosores de los componentes y la disposición de los medios de conexión. Estos son esenciales para la geometría delgada de la carcasa y el bajo uso de materiales.
Prefabricación robótica
La carcasa de madera del pabellón alcanza 30 metros de luz con un peso de 38 kg/m2.
Las piezas individuales reducen significativamente el peso y el material, pero también aumentan el número de componentes, por ello la búsqueda de una mayor eficiencia de los recursos va acompañada de la producción automatizada de robots que construyen cada una de las piezas del caparazón.
Cada una de las 376 piezas están fabricadas con una plataforma robótica portátil de producción de madera fabricado por la ICD de Stuttgart y el BEC GmbH. Dicha plataforma contiene dos robots de alta resistencia. La flexibilidad de estos robots industriales permite la integración de todos las fases de prefabricación de las piezas de la carcasa del pabellón dentro de una única producción.
Para minimizar el consumo de material y el peso, cada pieza de madera está formada por dos paneles delgados que unen unas vigas de borde en la parte superior e inferior, formando así piezas de madera huecas. Esta abertura en la placa inferior permite el acceso de las conexiones de los pernos ocultos durante el montaje.
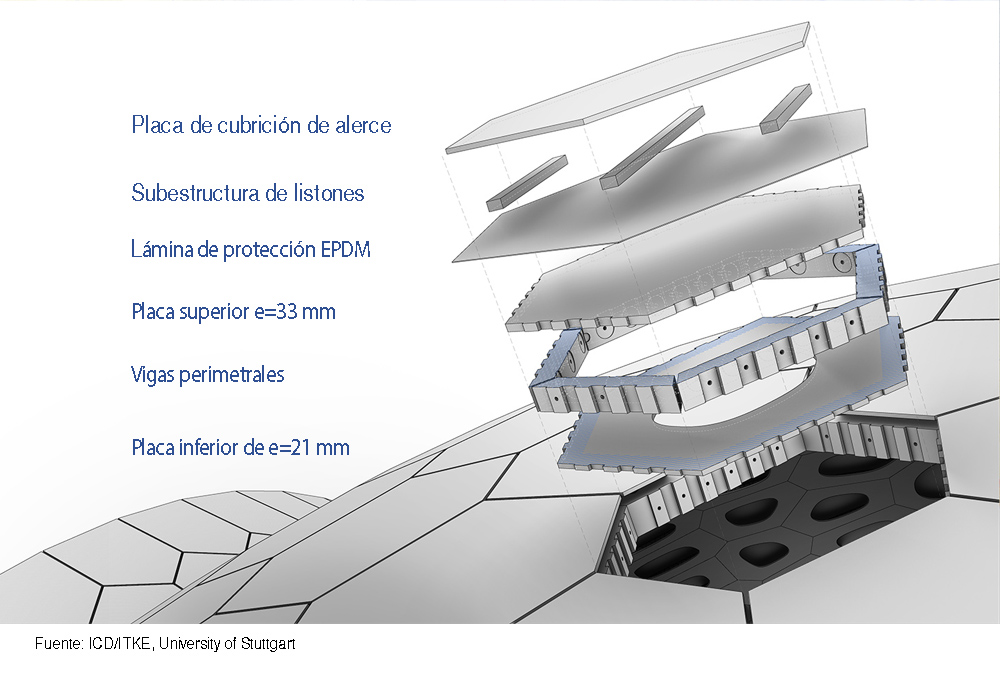
La fabricación robótica consta de dos fases:
- Fase inicial: dura aproximadamente 8 min, consiste en unir con adhesivo los paneles y vigas de madera que constituyen las piezas segmentadas, además de la fijación temporal con clavos para el proceso de secado.
- Segunda fase: durante 30 minutos, con alta precisión, se fresan las piezas ensamblada individualmente para las conexiones y aberturas de las articulaciones.
Todo este proceso está completamente automatizado, controlado por 2 millones de líneas que se generan instantáneamente con el modelo del ordenador. Esta precisión es muy importante para el montaje rápido y fácil del caparazón de madera.
Construcción.
Uno de los aspectos más conflictivos del proyecto es la cimentación. La fabricación de la carcasa admite errores submilimétricos. Sin embargo, la cimentación acepta imprecisiones de más de un centímetro. Para subsanar esta diferencia de precisión, se ha optado por diseñar las piezas próximas a la base con un margen de admisión de pequeñas inexactitudes. La unión de las piezas con la cimentación se realiza con pernos.
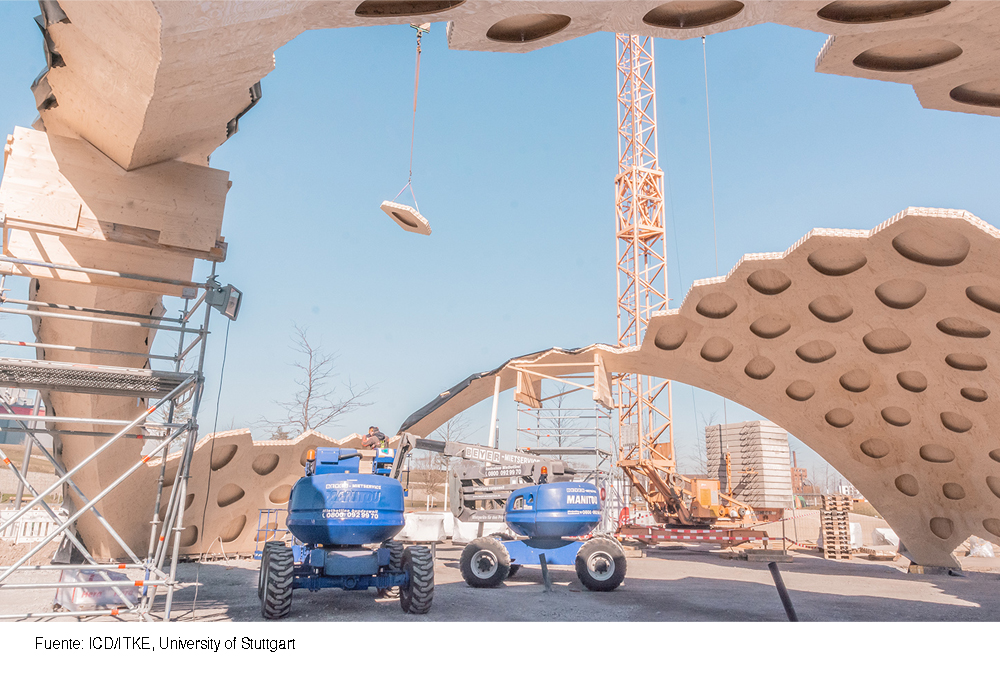
Para la unión de las piezas individuales, sin andamios o encofrados, fue necesario el trabajo de dos artesanos durante 10 días. Estas piezas están conectadas por pernos reutilizables, mecanismos que siguen los principios morfológicos de los bordes de las placas de erizo de mar. Un caso de unión especial del proyecto es la curva de los tres arcos, en este punto las conexiones se realizan con tornillos de madera.
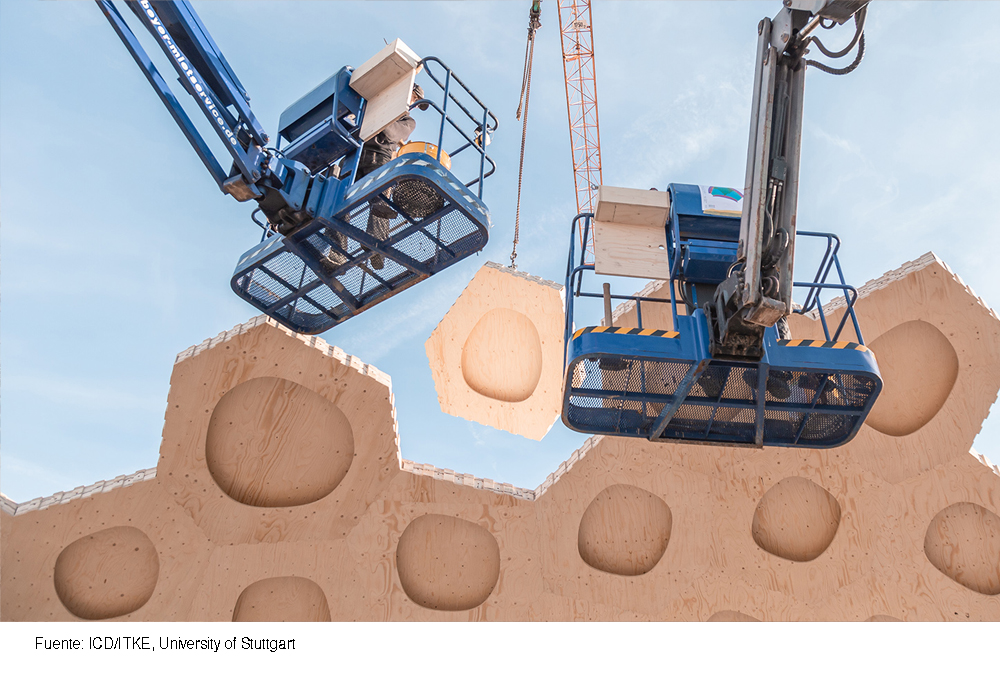
Por último, en el interior, la iluminación del pabellón es continua, se realiza de una pieza otra a través de las perforaciones existentes que se ejecutan en la fase de prefabricación robótica. En el exterior, el revestimiento del pabellón se materializa con unas chapas de madera de alerce sobre una subestructura de listones reciclados. La protección al sol y al agua del pabellón se garantizan con la utilización de lámina EPDM.
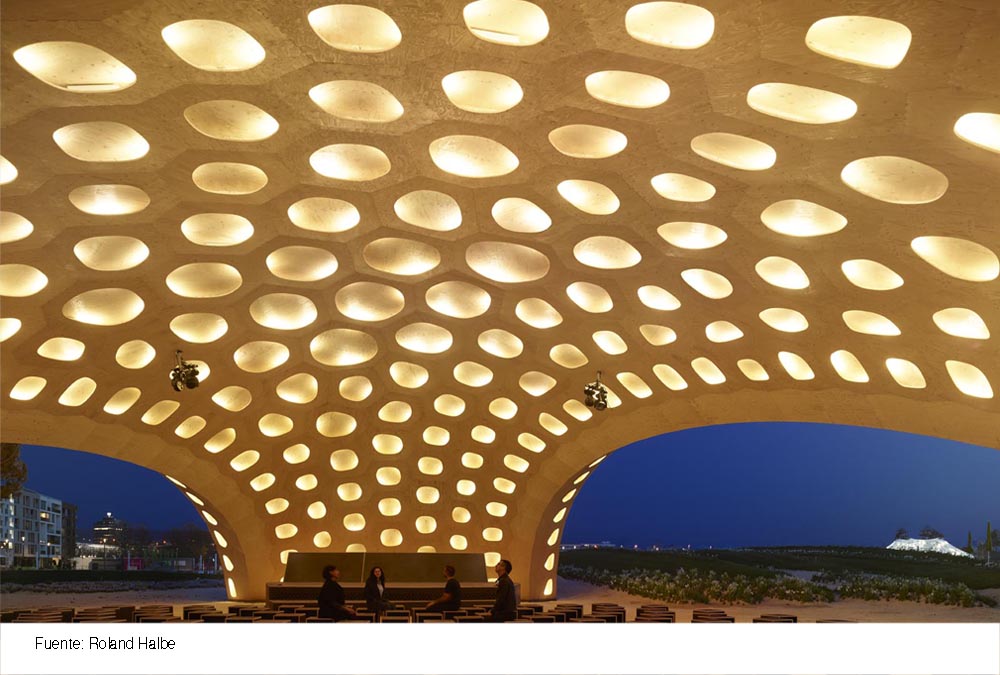
FORUM HOLZBAU España.
Si os ha parecido interesante este proyecto, y queréis saber más sobre la evolución de la construcción en madera tanto en nuestro país como en otros, os recomendamos asistir a la II edición del FORUM HOLZBAU ESPAÑA, los días 4 y 5 de junio, en el Palacio de Congresos Baluarte de Pamplona.
REFERENCIAS BIBLIOGRÁFICAS.
Menges, A., & Schwinn, T. (2012). Manufacturing Reciprocities. Architectutal Design, 82(2), 118-125.
Menges, A. (2013). Morphospaces of Robotic Fabrication. In S.Brell-Çokcan & J.Braumann (Eds.), Rob | Arch 2012 (pp.28-47). Vienna: Springer Vienna.
Menges, A., Knippers, J., Wagner, H.J., & Sonntag, D. (2019). BUGA Holzpavillon – Freiformfläche aus robotisch gefertigten Nulltoleranz-Segmenten. 25 Internationales Holzbau-Forum /HF 2019, 219-138.
Editores del post: Maderayconstruccion
Si te gustó el post, estaría genial que la compartas en tus redes sociales.
A su vez, te animamos a seguirnos en las siguientes redes:

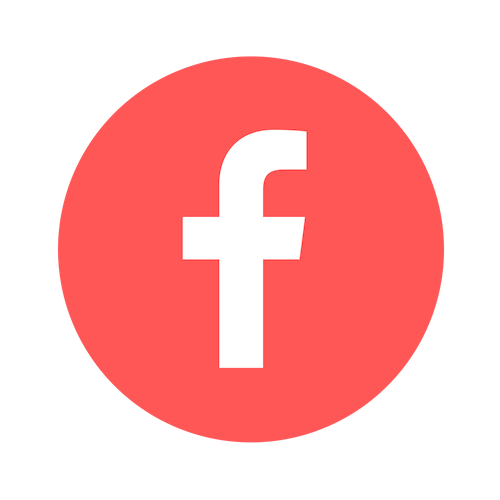
Irene Jimeno – Toca Madera
También puede interesarte